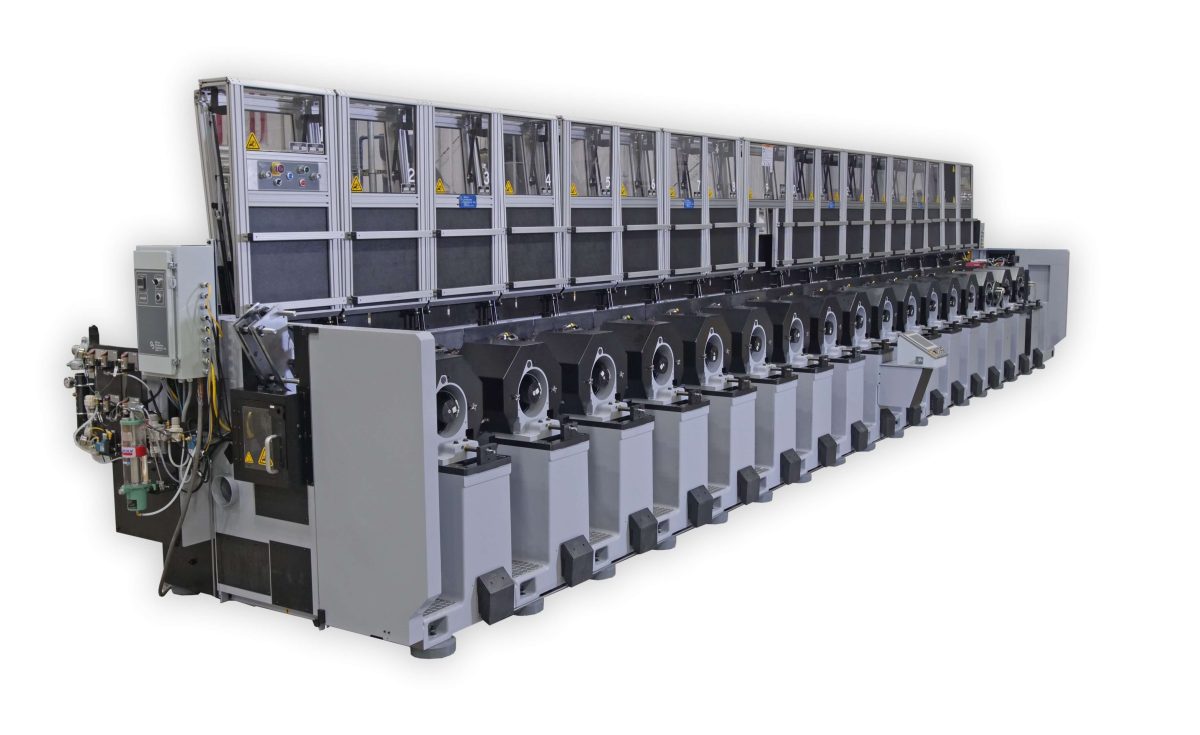
The 595VE Necker
- Necker
The 595VE Series is engineered for longevity, offering the highest cost-effective setup, continuously operating up to 3,000 cpm.
Key Benefits
With longevity and reliability at the forefront of the design process, the 595VE Necker series has been engineered to consistently produce high-quality cans. Available in two models, the K and SK, it is capable of producing 2,400 and 3,000 cpm, respectively. With its modular design, the 595VE Necker series is easy to rebuild and maintain, ensuring longevity and reliability. The machine’s turret has been standardized, streamlining operations and reducing the time required for can-size changeovers. Overall, the 595VE Necker series is an efficient and cost-effective solution for customers looking to produce high-quality cans.
The machine offers various features, including flanging, reforming, reprofiling, light tester, and inspection modules. It’s also equipped with an Intelligent Manufacturing System (IMS) and High-Speed Selective Sorter (HS3) that provide dynamic quality control and rapid sampling while troubleshooting upstream problems. The 595VE SK model’s spring-loaded cam followers help reduce size changeover times, increasing efficiency and cost-effectiveness. Additionally, Belvac’s Intermediate Infeed enhances flexibility and efficiency while saving equipment cost and floor space requirements.