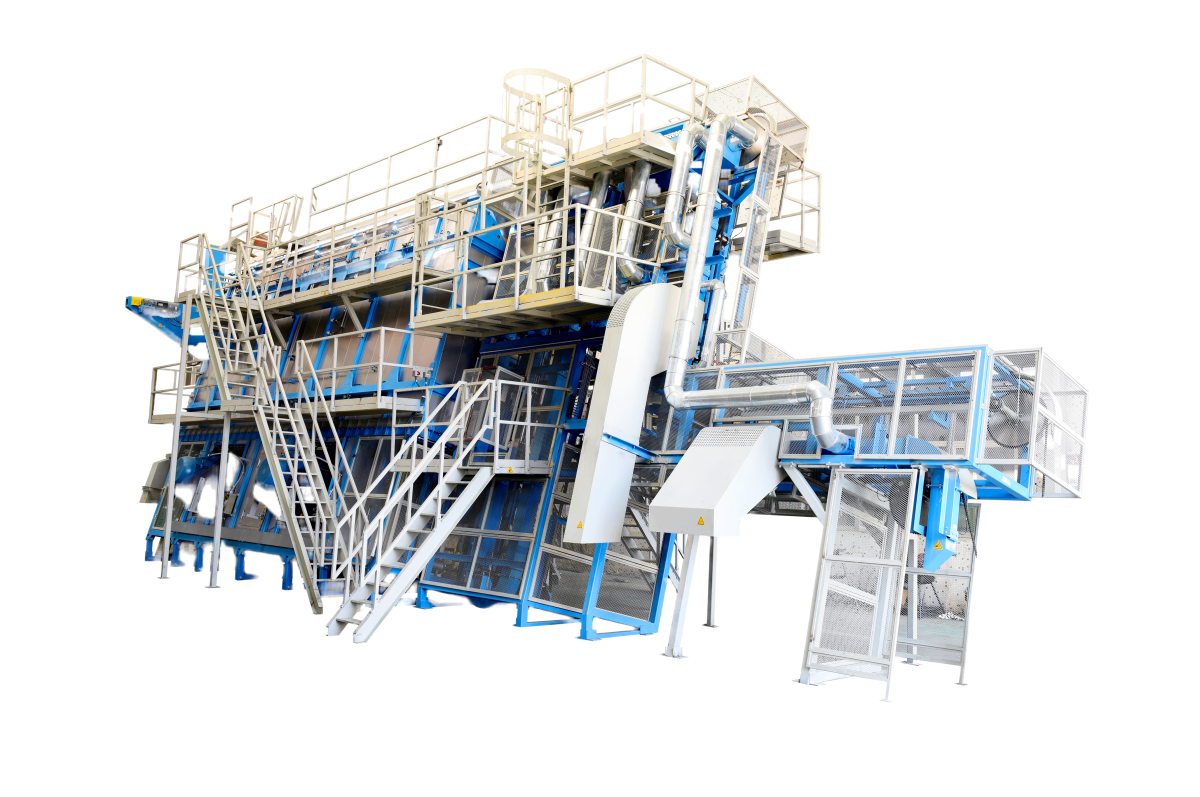
Pin Oven
- Can Making Machinery
Designed to maximize ease of operation, the ARC Pacific Pin Oven features high accessibility, temperature uniformity, and minimized gas consumption.
Key Benefits
Designed to maximize ease and efficient operation, the ARC Pin Oven has a single heat zone configuration that features temperature uniformity allowing the can to be cured in either ten or twelve passes. The cans are carried through the Oven to cure the freshly applied label from the Decorator via the pin chain that maximizes can stability. Made with a sturdy steel frame and compact machine footprint, and platform on top of the Oven to maintain the return chain pass, the Oven features high accessibility for safe and efficient maintenance.
The front frame is designed with physical space for your Bottom Rim Coater in addition to the chain tensioning unit. An optional two pass cooling chamber, equipped with VFD fans, helps to reduce overall heat loss into the plant. Following the cooling chamber, the cans are discharged via the VFD Vacuum Pin Stripper which transfers the cans off the pin chain and onto traditional conveyance. The Pin Stripper is designed for label camera inspection installation. ARC Pacific’s 6-inch insulated wall technology helps the Oven retain heat efficiently while also minimizing overall gas consumption. The 2-inch external safety cool walls offer safer conditions for operators.
The Pin Oven maximizes process efficiency with its VFD recirculation fans that adapt to line speed ensuring the correct amount of heat is transferred to the can to cure the label. The pin chain lubrication unit ensures a smooth and constant operation. When fitted with an oil mist eliminator, the excess oil mist is extracted from the air via a centrifugal filter. The automatic bearing lubricator allows for safer operation and less machine maintenance.
Additionally, the Pin Oven is equipped with a more robust monitoring system that has been upgraded to perform real-time monitoring of machine pressures, dynamic balancing and help optimize gas efficiency. The Exhaust Orifice Monitor measures the amount of air exiting the Oven in real-time, so operators can control air flow balance and exhaust rates, ensuring all operations adhere to EHS guidelines while also minimizing gas consumption.